Produktentwicklung: Methoden und Massnahmen zur Kostenbeeinflussung
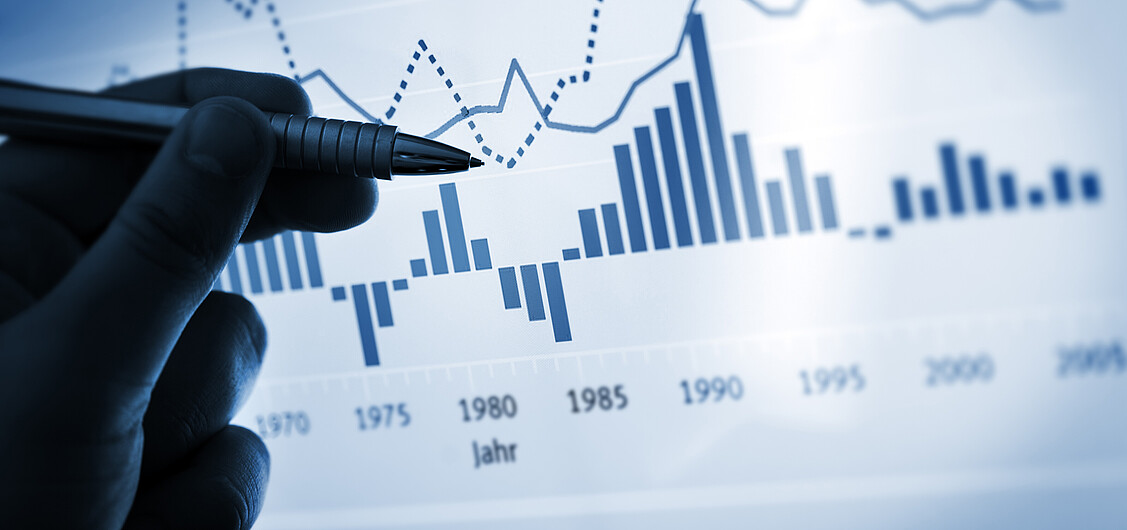
Passende Arbeitshilfen
Einleitung
Ein grundlegendes Dilemma hierbei ist der Umstand, dass während der Entwicklung und Konstruktion die späteren Herstellkosten der Produkte zu einem hohen Anteil festgelegt werden. Dabei wird die Kostenstruktur einer Komponente oder eines Produkts regelmässig durch die Stückliste und den Arbeitsplan dokumentiert, welche durch die Produktentwicklung und Produktindustrialisierung fertiggestellt werden. Während des anschliessenden Produktionsprozesses kann dann nur noch wenig Einfluss genommen werden auf die Kostenentstehung. Durch die hohen Produktionsmengen entlang des Lebenszyklus eines Produkts verlagert sich der Kostenanfall daher vor allem auf die Fertigungsphase.
Produktentwicklungsprozess und Kostenrechnung
Der Produktentwicklungsprozess umfasst alle Aktivitäten, die zur Entwicklung und Produktion eines Produkts notwendig sind. Die Produktentwicklung und -erstellung erfolgt als Zyklus entlang verschiedener Phasen, von der ersten Idee für ein neues Produkt über die Erstellung eines Prototyps, den Serienstart bis zur Auslieferung des fertiggestellten Produkts an die Kunden. Dabei handelt es sich um den konventionellen, grösstenteils sequenziellen Ablauf von Vertriebs-, Entwicklungs- und Produktionstätigkeiten. Der Lebenslauf eines Produkts geht jedoch über die Produkterstellung hinaus und endet mit dessen Entsorgung (Ehrlenspiel/Meerkamm, 2013, S. 161–163).
Im Zusammenhang mit der Produktentwicklung übernimmt die Kostenrechnung vor allem drei wesentliche Ziele:
-
die laufende Kontrolle der Wirtschaftlichkeit durch den Vergleich der anfallenden Kosten mit der erstellten Leistung,
-
die Vorkalkulation, d.h. die Ermittlung der voraussichtlichen Kosten einer Auftragsabwicklung, und
-
die Nachkalkulation, d.h. die Ermittlung der tatsächlich angefallenen Kosten einer Auftragsabwicklung.
Damit diese Aufgabe der Kostenrechnung in zweckmässiger Weise erreicht werden kann, muss die Kostenrechnung die Erfassung, Verteilung und Zurechnung der einzelnen Kosten übernehmen und diese den Kostenträgern möglichst verursachungsgerecht zuordnen.
Reduktion der Herstellkosten
Die Herstellkosten bilden den Kern der durch Produkte verursachten Kosten. Sie sind direkt dem Produktionsprozess zurechenbar und bestehen hauptsächlich aus Material-, Fertigungs- und Prüfkosten. Zusätzlich zu diesen Herstellkosten gibt es Aufwendungen, welche nicht direkt dem Produktionsprozess angerechnet werden können, wie beispielsweise die Kosten der vorgängigen Produktentwicklung oder die Vertriebs- und Verwaltungskosten. Diese Kosten bilden zusammen mit den Herstellkosten die Selbstkosten.
Wird die ganze Lebensdauer eines Produkts betrachtet, kommen weitere Kosten hinzu. Dies können einmalige Kosten für die Entwicklung eines Prototyps oder solche für die Inbetriebnahme oder auch spätere Entsorgung sein oder mehrmalige Kosten für Betrieb, Wartung und Instandhaltung. Zusammengefasst ergeben sie die gesamten Lebenszykluskosten eines Produkts (Ehrlenspiel et al., 2014, S. 7–8).
Zu beachten ist dabei, dass die Materialkosten definitionsgemäss sämtliche Kosten des Einkaufs enthalten. Dies sind Ausgaben für Rohmaterial, Halbzeuge, Normteile und fremdbezogene Bauteile (Kaufteile). Dabei umfassen die Materialkosten die gesamten Anschaffungskosten, welche neben dem Produktpreis der Zulieferer auch Transport- und Beschaffungskosten, Einfuhrabgaben und Zölle betreffen.
Passende Produkt-Empfehlungen
Zur Kostenoptimierung des Produktentwicklungsprozesses, bei dem die späteren Herstellkosten des Produkts im Mittelpunkt stehen, ist es von zentraler Bedeutung, dass bereits frühzeitig ermittelt wird, wo und wofür welche Kosten der Produkte entstehen und wie diese Kosten beeinflusst werden können. Hierbei gilt das Dilemma zu beachten, dass die Produktentwicklung nur einen kleinen Teil der Produktkosten direkt verursacht, wobei sie jedoch trotzdem massgeblich die Kostenentstehung verantwortet, da ein Grossteil der späteren Herstellkosten während der Entwicklungs- und Konstruktionsphase festgelegt wird.
Die technischen Abteilungen Entwicklung, Arbeitsvorbereitung und Fertigung bestimmen zusammen ca. 90% der gesamten späteren Produktkosten. Dagegen fällt die Kostenentstehung jedoch grösstenteils im Einkauf und in der Fertigung an. Im Hinblick auf eine Optimierung der Produktentwicklung zur Erzielung von kostengünstigeren Produkten ist der grosse Unterschied bei der Entwicklung und Konstruktion zwischen Kostenfestlegung und Kostenverursachung von Bedeutung. Somit gilt es, während der Produktentwicklung nicht primär Entwicklungskosten zu sparen, sondern mit erfahrenen und qualifizierten Mitarbeitern die Produkte so zu konstruieren, dass sie unter Berücksichtigung der Kundenerwartungen später möglichst kostengünstig produziert werden können (Ehrlenspiel et al., 2014, S. 14–16). Diese Abbildung hier veranschaulicht diesen Zusammenhang.
Daraus ergibt sich: Was zu Beginn beim Planen und Entwickeln versäumt oder falsch gemacht wurde, lässt sich im späteren Verlauf kaum mehr korrigieren. Jede technische Entscheidung ist auch eine Festlegung der späteren Herstellkosten, weshalb bereits zu Beginn das Bewusstsein für die Kostenfestlegung im Produktentwicklungsprozess vorhanden sein sollte.
Für die Reduktion der Herstellkosten, die sich aus den Material- und Fertigungskosten zusammensetzen, ergeben sich in der Praxis die Ansatzpunkte, die hier abgebildet sind.
Grundsätzlich ergeben sich Einsparungsmöglichkeiten beim Material, in der Fertigung oder in der Montage der Bauteile sowie bei der Qualitätsprüfung.
Von hoher Wichtigkeit ist hierbei die Produktkalkulation, mit der die Herstellkosten und Selbstkosten der Produkte oder Kundenaufträge bestimmt werden. Grundsätzlich kann zwischen der Vor- und der Nachkalkulation unterschieden werden. Bei der Vorkalkulation wird vor der Auftragserteilung bzw. vor dem Beginn der Herstellung eine Plankalkulation der Herstellkosten bzw. der Selbstkosten durchgeführt.
Diese basiert zu Beginn regelmässig auf geplanten und geschätzten Kostendaten und dient meist auch als Grundlage für Offerten oder Preisverhandlungen. Bei der Nachkalkulation werden dagegen die tatsächlichen Kosten nach Abschluss des Auftrags oder nach der Fertigung eines Produkts berechnet. Die Nachkalkulation dient damit vor allem der Kosten- und Erfolgskontrolle.
Durch ein Kostenmanagement während der Produktentwicklung sollen die späteren Kosten der Produkte beeinflusst werden. Es umfasst deshalb verschiedene Methoden und Verfahren, welche Einfluss auf die Kosten nehmen, um eine Reduzierung der Herstellkosten zu erreichen. Alle Methoden des Kostenmanagements zielen darauf ab, entweder die Kosten direkt zu senken oder indirekt eine Kostensenkung zu bewirken. Die bekanntesten Methoden werden nachfolgend dargestellt:
Zielkostenrechnung (Target Costing)
Mit dem Einsatz des Target Costings wird versucht, eine den Kundenerwartungen entsprechende Reduktion der Produktkosten umzusetzen, die ein Produkt während seines Lebenszyklus verursacht. Das Ziel des Target Costings ist es, das gesamte Unternehmen an den Anforderungen des Markts auszurichten. Durch die Abstimmung der aus der Markt- bzw. Kundenperspektive erlaubten Kosten (“Allowable Costs”) mit den voraussichtlichen Produkt-Standardkosten sollen Zielkosten (Target Costs) bestimmt werden, die es durch geeignete Kostensenkungsmassnahmen während der Produktentwicklung zu erreichen gilt.
Der Ablauf des Target Costings gliedert sich in vier Phasen. Die Abbildung hierzu finden Sie hier.
Für die Herleitung der Zielkosten wird ausgehend vom durchschnittlichen Zielpreis für ein Produkt die Zielmarge des Unternehmens in Abzug gebracht. Ebenfalls werden solche Gemeinkosten in Abzug gebracht, die nicht im Rahmen der Produktentwicklung für Einsparungsmassnahmen zur Verfügung stehen. Dabei handelt es sich zumeist um anteilige Verwaltungs- und Vertriebsgemeinkosten. Übrig bleiben die Ziel-Herstellkosten (Target Costs), welche unter Berücksichtigung der Kundenerwartungen über die Produktfunktionen auf einzelne Produktkomponenten aufgespalten werden, sodass die Zielkosten auf einzelne Komponenten und Baugruppen übertragen werden. Im Anschluss wird durch Produktänderungen, z.B. beim Funktionsumfang oder bei physikalischen Produkteigenschaften, durch die Entwickler zielgerichtet für die Komponenten nach Einsparungen geschaut, deren Kosten noch die festgelegten Zielkosten überschreiten.
Im folgenden Beispiel eines Gefrierschranks übersteigen die Standard-Herstellkosten für das Kühl- und Gefrierfach sowie diejenigen für die Bedienungselemente die vorgegebenen Zielkosten, während die Standardkosten für das Gehäuse sogar unterhalb der “erlaubten” Zielkosten liegen. Somit hat die Produktentwicklung einen Kosteneinsparungsbedarf von CHF 90.00 bei den Produkt-Herstellkosten zu erreichen, welcher sich im Bereich der Material- und/oder Fertigungskosten auswirken muss.
Messgrösse/Komponente | Standard-Herstellkosten (CHF) | Zielkosten (CHF) | Korrekturbedarf (CHF) |
---|---|---|---|
Kühl- und Gefrierfach | 450.00 | 376.12 | 73.88 |
Gehäuseform und -grösse | 380.00 | 386.75 | –6.75 |
Bedienungselemente | 110.00 | 87.13 | 22.87 |
Summe | 940.00 | 850.00 | 90.00 |
Insofern wird bei der Methode des Target Costings von Beginn an mit Kostenzielen gearbeitet und somit auch kostenorientiert entwickelt.
Wertanalyse (Value Analysis)
Das Konzept der Wertanalyse zielt neben einer Realisierung von Kosteneinsparungen darauf ab, den Produktnutzen (Wert) für die Abnehmer dadurch zu steigern, dass die Produktfunktionen und/oder die Leistungsabgabe des Produkts im Verhältnis zu den produktbezogenen Kosten verbessert wird. Hierzu wird ein systematisches Vorgehen gewählt, das auch die Zusammensetzung der Materialien und Teile des eigenen Produkts im Vergleich mit Wettbewerber-Produkten analysiert, um bereits in den Materialkosten Einsparungspotenziale zu identifizieren. Hierzu wird eine Dekonstruktion des Produkts vorgenommen und anschliessend die Notwendigkeit der verschiedenen Materialien und Bauteile beurteilt. Vor allem die Veränderung oder der Ersatz bisheriger Materialien und Bauteile durch kostengünstigere Alternativen bei gleicher oder höherer Nutzenabgabe kann ein Ergebnis der Wertanalyse sein. So kann beispielsweise der Ersatz von Stahl-Zahnrädern durch Kunststoff-Zahnräder in einem Produkt nicht nur zur Kostenreduktion beitragen, sondern ebenfalls zur Gewichtsersparnis und zur höheren Wartungsfreundlichkeit bzw. zu einer geringeren Reparaturanfälligkeit.
Mittels Kreativtechniken wie z.B. Brainstorming soll ein Wertanalyse-Team Ansatzpunkte für Kosteneinsparungen sammeln und diese anschliessend analysieren und bewerten. Da die Einsparungen keine Hauptfunktion des Produkts einschränken sollen, ist die Einstufung der Funktion in Haupt-, Hilfs- bzw. unnötige Funktionen von grosser Bedeutung. Die Wertanalyse ist ein Projekt mit einem Anfang und einem Ende. Sie forciert einmalig umgesetzte Einsparungen innerhalb der Produktkosten und kann zu beliebigen Zeitpunkten im Produktlebenszyklus wiederholt werden.
Die Wertgestaltung (Value Engineering) gilt als eine spezifische Form der Wertanalyse, welche sich auf noch nicht realisierte Produkte und Produktkomponenten bezieht, während die Wertverbesserung bei bestehenden Produkten zum Einsatz kommt. Bekannte Beispiele für erfolgreiche Wertanalyse bei Produkten liefert vor allem die Automobilindustrie, wo durch die Verwendung von Gleichteilen bzw. Standardteilen und eine Plattform-Strategie für mehrere Modelle zur Reduktion von Bauteilen und damit ebenfalls zur Verringerung von Komplexitätskosten bei gleicher Leistung für die Kunden erreicht wurde.
Fazit
Für kostenorientierte Entwicklungsprojekte oder Kostensenkungsprojekte gelten grundsätzlich dieselben Erfolgsfaktoren: Eine optimale Lösung zur Erfüllung der technischen Anforderungen und der wirtschaftlichen Zielkosten unter Berücksichtigung der konstruktiven Möglichkeiten lässt sich nur durch einen wechselseitigen Prozess zwischen Konstruktion und Kalkulation erreichen. Vor allem dann, wenn während der Produktentwicklung Differenzen zwischen den technischen Interessen und Vorhaben der Entwickler einerseits und den Kostenzielen des Controllings andererseits vorliegen, ist eine interdisziplinäre Besetzung der Projekt-Teams von hoher Wichtigkeit. Dabei gilt es planvoll und frühzeitig im Entwicklungsprozess die Bedeutung einzuhaltender Kostenziele zu verankern und in Form von Kostenvorgaben den Teilprojekt-Verantwortlichen anzugeben, da nur so die Einhaltung der Kostenziele für das Gesamtprodukt erreicht werden kann.